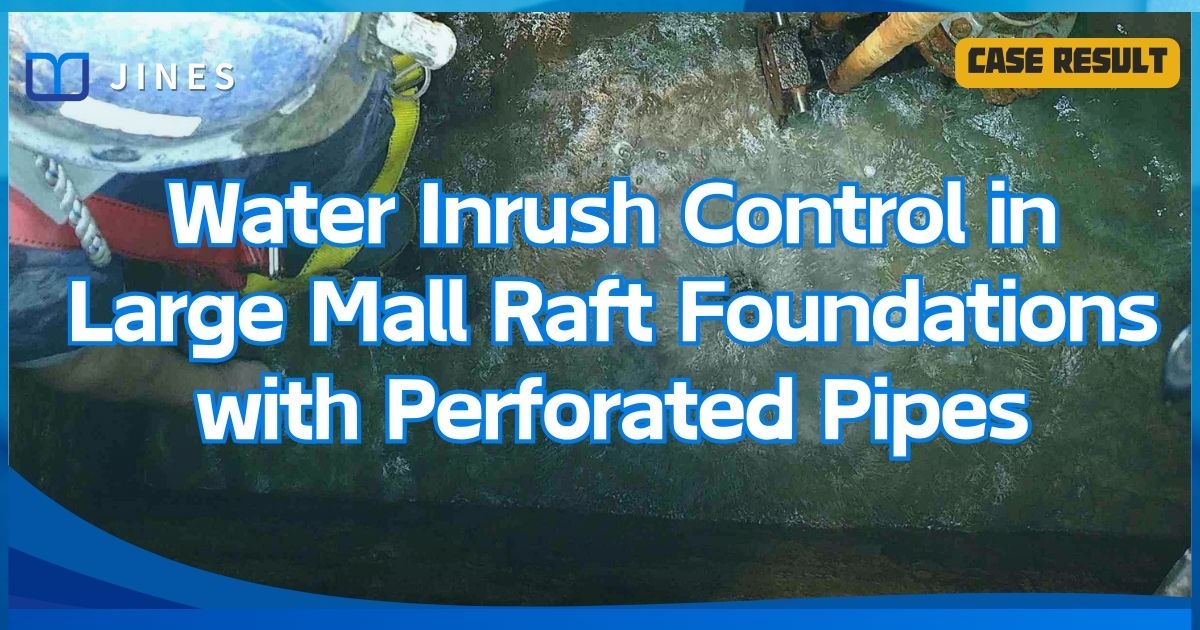
WATER INRUSH CONTROL IN OPERATIONAL LARGE SHOPPING MALL
RAFT FOUNDATIONS WITH PERFORATED PIPES
Double-tubing grouting method for sealing underground cavities
―
1. Project Background
In a large operational shopping mall, the raft foundation’s water tank had been discharging a significant amount of water for an extended period.
Due to the increasing volume of drainage, the management was concerned about potential damage to the foundation structure that could compromise safety. Additionally, they aimed to reduce recurring expenses related to water pumping.
To address these issues, they commissioned a professional firm with expertise in foundation water-stopping and reinforcement to conduct an on-site survey, propose a solution, and, following evaluation, implement the necessary measures.
―
2. Solution
Based on the site survey and inspections of the raft foundation water tanks, it was discovered that one of the water tanks had a significant water inrush point, estimated at around 800 liters per minute.
Upon sealing off the water tank’s connecting pipe and draining the accumulated water inside, it was found that the outflow point was a 3-inch PVC pipe buried at a depth of approximately 70 centimeters.
Consultation with maintenance personnel from earlier years revealed that several years ago, the foundation had experienced a rupture with water infiltration, and the drainage pipe was installed to prevent the crack from expanding.
At that time, the outflow was only about 200 liters per minute. However, over time, the subsoil’s fine particles were eroded, leading to a significant increase in the outflow.
To effectively seal the water inrush point, the water-stop plan was as follows:
1. Install a water-stop case around the pipe opening and then use a drilling machine to penetrate the raft foundation base.
2. Employ a double-tubing grouting method to perform water-stop grouting of the subsoil beneath the PVC pipe.
3. Backfill grout inside the 3-inch PVC pipe.
4. Repair and restore the raft foundation base structure.
―
3. Works Design
The structure’s excavation face was approximately at GL-11.4 meters. Within the foundation, the range of GL-12.8 meters to GL-13.9 meters consisted of gravelly silty sand layers, below which there was a continuous muddy sandstone with thin layers of mudstone.
Since beneath the foundation was a highly permeable gravel layer, the groundwater level was around GL-5.0 meters, and one side of the site was adjacent to a river, ensuring an abundant groundwater supply.
Based on the characteristics of this project, the construction design was as follows:
- Install four grouting holes around the water inrush point with waterproof boxes at the hole openings to prevent direct penetration of the foundation and a significant water influx, which could lead to a rapid reduction in buoyancy and potential structural damage.
- Use the double-tubing grouting method in combination with instant and slow-setting, long-acting low-sodium silicate sodium chemical grout to achieve cross-grouting. The grouting depth extended from beneath the foundation to GL-14.0 meters, reducing the permeability coefficient of the gravel layer beneath the foundation to below 1×10-5 cm/sec in the vicinity of the water leakage point.
- Fill the interior space of the PVC pipe with long-acting FLW rapid-setting cement chemical grout to effectively seal the water inrush pathway.
- Maintain grouting pressure not exceeding the initial pressure by more than 200 kPa as a principle to prevent further damage to the partially compromised concrete foundation.
- After completing waterproofing and backfill grouting, remove the early backfilled cement mortar and low-quality concrete around the PVC pipe. Clean the area and repair the foundation with resin mortar.
- Observe the repaired location for at least one week to ensure that there is no recurrence of water infiltration.
- After confirming that the water influx sealing objectives have been met, restore the mutual connectivity between the water tanks. Regularly monitor the raft foundation’s water pumping frequency and any abnormal water discharge conditions.
―
4. Works Process
Due to the extremely fast groundwater flow beneath the water inrush point, during the double-tubing SSA chemical grouting process, the quick-setting grout material had a setting time set between 5 to 10 seconds, and the slow-setting grout material was set between 10 to 20 seconds. The grouting was carried out in a two-stage inverse sequence, at intervals of 0.5 meters, with a flow rate of 16 liters per minute.
In the event that the pressure for the slow-setting grout material could not be increased, it was switched to the quick-setting grout material until the pressure rose to 100-200 kPa. Then, it was switched back to the slow-setting grout material for injection, aiming to achieve the goal of uniformly reducing the permeability coefficient of the subsoil.
―
5. Results
Using the double-tubing grouting method in combination with SSA chemical grout and FLW cement chemical grout, many successful experiences had been accumulated in reducing subsurface permeability, filling underground voids, managing groundwater seepage during foundation excavation, and sealing off water leakage in foundations.
After implementing the construction design for this project, the water seepage from the tanks completely stopped.
Following a contractual observation period of over a week, there were no instances of water leakage at the repair locations.
After unblocking the connecting pipes in the water tanks and restoring their interconnection, the wastewater pump frequency consistently met the original design requirements. This work was successfully completed.
―
・More Construction Result Sharing
Contact us:+886 2769-2355