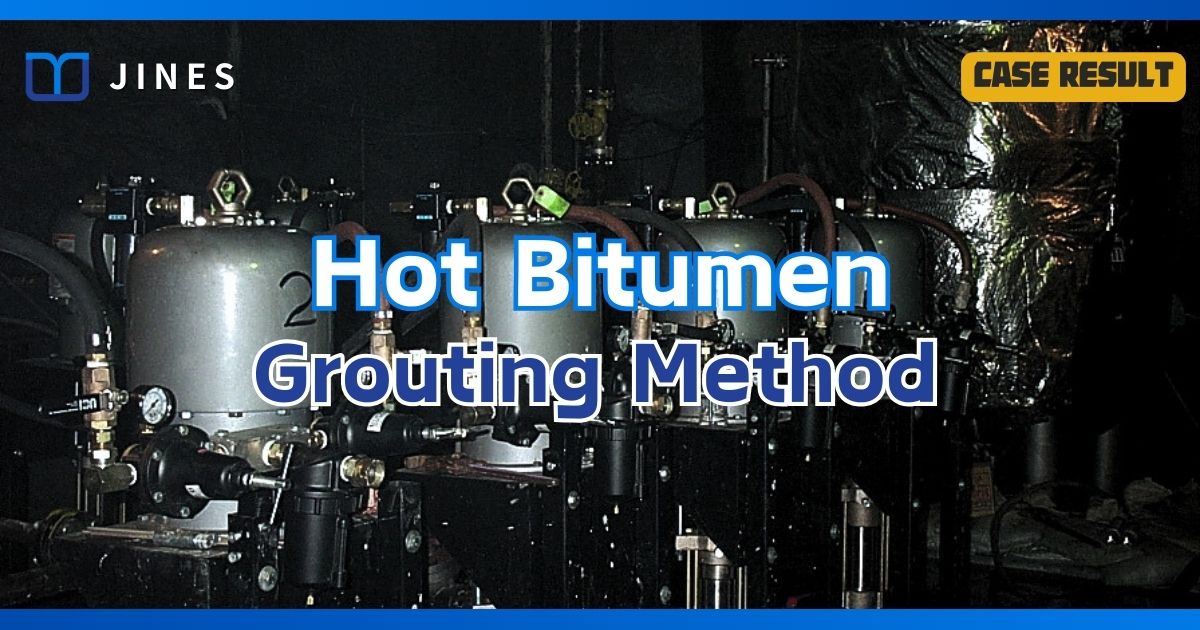
Hot Bitumen Grouting Method
1. What is Hot Bitumen Grouting Method?
Hot bitumen grouting is a specialized technique that utilizes a specific type of bitumen that exhibits a liquid state at high temperatures and rapidly increases in viscosity when in contact with groundwater or as it cools.
This method is employed in areas with flowing water, high volume water inrush, or areas of extensive leakage to effectively seal off and fill voids.
The process involves injecting the hot bitumen into rock formations, structural cracks, or weak geological layers by utilizing the steam pressure generated during the grouting process.
This allows the liquid bitumen to flow into the desired areas and form a waterproof layer, effectively blocking water infiltration.
Hot bitumen grouting is characterized by its “later in, goes first” nature, meaning that the hot bitumen is injected after it is melted and can flow through previously solidified bitumen, effectively filling various large and small cracks.
This method ensures comprehensive sealing of water inrush and achieves the desired waterproofing effect.
―
2. Hot Bitumen Grouting Principle
In traditional grouting methods for addressing groundwater flow, it is often challenging to effectively achieve solidification and water stoppage due to factors such as high flow velocities or other difficulties, which can result in the loss or dilution of grouting materials.
The solidification process of bitumen grouting is primarily controlled by temperature.
When flowing water comes into contact with hot bitumen grouting material, the temperature of the material decreases, causing the viscosity to rapidly increase (bitumen viscosity is highly sensitive to temperature changes).
As a result, the areas in contact with flowing water quickly solidify.
―
3. Hot Bitumen Grouting Applications
―
4. Key Execution Points
- Site Investigation (Drilling and Equipment Installation)
- Equipment Mobilization and Installation
- Heat Insulation Facilities
- Material Delivery (Insulated Hot Bitumen)
- Drilling (Location/Angle/Pressure Relief Holes)
- Thermal Oil and Rupture Disc
- Pipeline and Environmental Preheating
- Hot Bitumen Grouting
- Site Temperature Monitoring (Grouting Material Dispersion Range)
- Supplemental Grouting and Pressure Relief Hole Sealing
―
5. Analysis of Advantages and Disadvantages Advantages :
- The grout’s solidification time is controlled by temperature, which is a physical reaction, eliminating the issue of reaction time gaps.
- Suitable for treating conditions involving water inrush.
Disadvantages:
- The viscosity of the grout varies with temperature, which can lead to poor uniform diffusion in the soil layer.
- Machinery and equipment need to operate at high temperatures, requiring careful management of construction safety measures.
―
6. Hot Bitumen Grouting Key Equipment
- Drilling Rig (Conventional drilling rig, Modified drilling rig)
- Grouting Pipe
- Grout Delivery Pipe (Heat-resistant)
- Heat Insulation Equipment (Materials)
- Heatable Storage Tank (Equipment side/Construction side)
- High-temperature Resistant Pump (Pneumatic or Mechanical)
- Heatable Oil Storage Tank (Circulating thermal oil, if required)
- Rupture Disc (Disposable pressure control valve)
- Pressure Relief Pipe (Including control valve)
- Monitoring Equipment (Temperature, Pressure, Flow rate)
- Site Monitoring Equipment (Temperature)
7. Common Materials for Hot Bitumen Grouting
– Water Inrush Sealing: Bitumen
– Ground Compaction Consolidation: Bitumen
―
8. Engineering Applications
―
9. Case Study – Water Inrush Control in Deep Excavation (Hot Bitumen Water-Stop Method) .
Water Inrush Treatment at Excavtion of Deep Strata:
-During the process of excavation, an exisiting inclined pipe was encountered, which resulted in water inrush. initially, only a small amount of water trickled through, but as the water carried fine particles such as silt and sand, it gradually formed a larger water channel through piping.
This process continued to erode and wash out larger amounts of fine particles.
-The water gushed out continuously at a rate of approximately 3.2 tons per minute through the water inrush hole, which was estimated to have had a diameter of around 35 centimeters, close to the ground surface.
―
Construction Results
Approximately 30 minutes after the start of the pouring, the reduction in water outflow could be visually observed; as the pouring time increased, the water outflow gradually continued to decrease.
After 2.5 hours of pouring, when 22 tons of material had been used, the water outflow was essentially eliminated; at the end of the pouring process at 3 hours, there was still a small amount of water being produced, estimated at about 10 liters per minute
―
10. Case Study – Sealing of Cofferdam Cracks
―
11. Case Study – Mountain Tunnel Water Inrush Treatment Background
· During the construction of the new Yongchun Tunnel, we encountered large amounts of spring water and severe suction collapses.
The maximum pressure of the spring water reached 50 Bar, with a flow rate of 80 tons/minute.
· With the hot bitumen grouting method, we poured bitumen at a high temperature of 230 degrees Celsius into the large spring water layer, successfully overcoming the spring water issue.
More than 3,000 tons of bitumen were used, and the maximum grouting pressure reached 100kg/cm².
Due to the remote location and large volume and pressure of grouting, this was a grouting job with a larger scale of equipment and higher complexity.
Work Situation
―
12. Case Study – Water Inrush Treatment for Existing Structures Work Situation:
– After the completion of a large shopping mall structure, there was a significant problem of spring water in the basement raft foundation water tank. This issue was successfully resolved by using the hot bitumen grouting method.
– In this project, due to the lower grouting pressure, all equipment was simplified and improved with modularization. Apart from the unchanged material properties, other aspects such as grouting design and equipment layout were all redesigned and planned.
―
Post-fill Waterproof Membrane:
For areas with damaged waterproof membranes or where it’s not possible to pre-lay the waterproof membrane before structure construction, bitumen is poured into the back of the structure to form an isolation layer, achieving the structure’s waterproof function.
During the construction process, thermocouples are used to measure the temperature of the structure body to ensure the uniformity of the grouting range.
―
・More Construction Result Sharing
Contact us:+886 2769-2355
Copyright ©Jines Construction Co.,Ltd