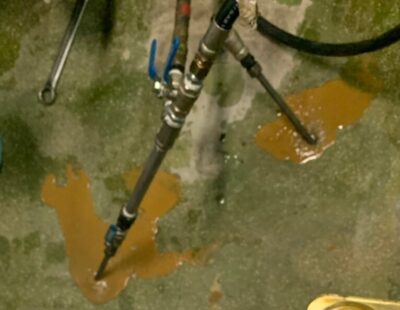
PREVENTIVE GROUTING REINFORCEMENT FOR INDUSTRIAL PLANT FOUNDATIONS HOLLOWING
Instant-setting resin grout filling and compression ground improvemen
1. Project Background
Yellow-brown and reddish-brown silty clay mixed with sandy silt was the strata beneath the foundations of an industrial plant.After a period of use, it was suspected that foundation hollowing had occurred. After conducting ground-penetrating radar detection, it was determined that there were localized voids, moisture infiltration and softness in the stratum below the foundations.
In order to avoid safety hazards caused by foundation subsidence in the future, the company was specially entrusted the to carry out ground improvement under the foundations to prevent accidents.
2. Solution
According to the ground-penetrating radar detection report, the formation voids and weak zones were distributed between GL.-0.25m ~ GL.-0.9m, and the plane positions were slightly scattered.In order to take into account the need for uninterrupted workshop production lines during the day, the location of large-scale production equipment in the workshop, the works process and the need not to cause any pollution after the works, the company proposed the following solution:
(1) Night works was adopted to avoid affecting normal production.
(2) Use non-solvent, non-toxic, non-swelling, instant-setting, rigid polyurethane resin for grouting.
(3) Micro-drilling grouting technology is adopted to reduce damage to the plant floor.
(4) First, improve the stratum below the pile footings of the structure to prevent disturbance and subsidence, and then improve the holes and weak zones under the floor according to the detection results of the ground-penetrating radar.
(5) Quality inspection before and after improvement is to be carried out using the DPM dynamic penetration tester.
3. Project Design
In order to ensure that the cavities under the foundation are fully filled and the weak zone is properly compressed and compacted, the relevant works design is as follows:
(1) Before grouting works, use the DPM penetration instrument to test at selected positions, and record the test results.
(2) When grouting, priority should be given to the improvement of the stratum below the piles, followed by the factory building surroundings, and finally the internal flooring.
(3) Stake out according to the design positions, and drill grouting holes with a diameter of 16mm and a depth of 1.0m. If there is existing equipment at this location, it is necessary to carry out verification to change grouting holes positions or increase the grouting holes.
(4) Bury a grouting pipe with diameter of 12mm to a predetermined depth.
(5) High-quality two-component rigid instant-setting polyurethane resin (TRIPOR-01) is to be used as filling and compressing grout.
(6) The grouting pressure is not to be more than (initial pressure + 3000kPa). During the grouting process, a laser level will be used to monitor the changes of the pile position and elevation of the floor in real time. If the change exceeds 1mm, the grouting operation should be suspended immediately.
(7) After the grouting is completed, perform the DPM soil penetration test again, and determine whether to perform supplementary grouting according to the test results.
4. Works Process
As this project was carried out at night, in order not to affect the normal operation of the workshop during the day, the drilling and filling positions and quantities had to be divided up and planned in detail every day.
The night’s ground improvement work was completed before production line started, and the works site thoroughly cleaned up and the grouting equipment relocated.As the company has rich experience in work such as road slabbing, flooring, tunnel inverts, and strata filling, reinforcement and jacking under building’s foundation, the operation of this project went smoothly, and the designed content was completed on schedule.
5. Results
This project utilizes the characteristics of “high-strength TRIPOR series instant-setting resin”, such as rapid setting, high bearing capacity, machine vibration absorption and repeated load bearing, etc., to successfully fill the gaps between the plant foundation and the stratum, and the stratum cavities.
Also, to achieve the compression and compaction of the weak zone. After completing all works designs and pouring work in sequence, the second DPM penetration test and ground-penetrating radar detection comparison, showed the holes and gaps under the foundation had been filled.
The bearing capacity of the stratum as estimated through the DPM test results, exceeded the design requirements and showed successfully completed preventive reinforcement of the industrial plant foundations.
・More Construction Result Sharing
Contact us:+886 2769-2355
PROTECTION OF VERTICAL SHAFT CAISSON CONSTRUCTION ADJACENT TO UNDERGROUND TUNNEL
將下載檔案寄至:
Copyright ©Jines Construction Co.,Ltd