
GROUTING ANTI-CORROSION TECHNOLOGY FOR THE FREE SECTION OF IN-PLACE GROUND ANCHORS
The Most Effective Way To Avoid Corrosion Of Existing Ground Anchors
1. Project Background
Grouting Anti Corrosion Technology : Taiwan’s mountain slopes account for about 70% of the total area. During project development, ground anchors are often used to prevent landslides.Whether the ground anchor itself can still maintain the design requirements after long-term use has become one of the key factors of engineering safety.
After several large-scale landslide disasters, the public authorities conducted a comprehensive physical examination of the ground anchors on both sides of the expressway and found that some of the free sections of the ground anchors were severely corroded.
In order to prevent the occurrence of disasters, the maintenance unit drew up plans for the reinforcement of damaged ground anchors and grouting protection for the free sections of the existing ground anchors to prevent continued corrosion.
―
2. Solution
Because the diameter of water molecules is only about 0.4 nanometers, as long as there are any permeable gaps in the free section of the ground anchor, the steel strands may be infiltrated and rusted after long-term use.
In the protection planning, in order to take into account the two elements of function and economy, the grouting material is optimized with cement-based grout and non-shrinking additives, and rust inhibitors are added to the cement (sand) grout to form a composite functional grout.
It also has the functions of preventing shrinkage cracks and generating an inactive protective layer on the surface of the steel strand.
―
3. Works Design
This grouting operation is divided into three main parts:
(1) Multi-section pouring of composite cement grout for free section of ground anchor. The grouting pumping pressure is less than or equal to 100kPa or the method of gravity flow infusion is adopted.
(2) The free section of the proximal end of the anchor seat is filled with composite cement grout, and the cement grout with a pressure ≦100kPa is pumped until it cannot be poured.
(3) Inspection of grouting results and restoration of protective cover.
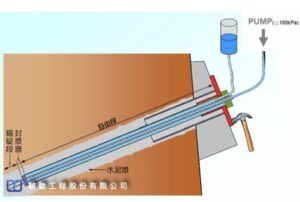
4. Works Process
The ground anchors are mostly located on the sidewalls of steep hillsides, and the inclined drilling design is adopted, and it is difficult to completely fill the free section with cement sand grout.
During the construction process, the composite functional grout material is injected from the bottom of the free section hole to the opening with a grouting pump until the accumulation of water and grout in the free section overflows from the anchor head.
The grout is left to settle before performing repeated pouring. When the low-pressure grouting is applied to 20~30cm below the anchor bearing plate, the gravity flow method is used to inject the cement grout under the anchor head until it is completely filled with grout and can no longer be injected.
5. Results
After multiple infusions of composite functional grout has filled the free section and completely hardened, the hardened cement grout is drilled with an electric drill for more than 10cm to test the hardness of the grout and detect whether there were cavities.
Then an electronic endoscope is inserted into the borehole to record the results of the grouting.If any of the cement sand grout is found to be poor in quality or the grout has not completely filled during the inspection process, holes are drilled from the anchor head to the unfilled area for supplemental grouting to ensure effectiveness of protection.
6. Experience
The corrosion of the steel tendons directly affects the life and effectiveness of the ground anchor.According to the inspection of ground anchors where landslides have occurred, it is found that the corrosion of the steel tendons in the fixed section after complete grouting protection is not obvious, but the free section with incomplete protection is severely rusted or even broken.
Due to the fact that it is not easy to infuse cement slurry into the free section of the ground anchor, it is recommended that the free section near the anchor head can be filled with a non-foaming PU elastic resin with good fluidity when the free section has been protected.
In addition to increasing working efficiency and achieving a complete filling effect, at the same time, the adhesion between the anchor and the concrete is improved by the waterproofing and bonding properties of the PU grout.
This prevents the surface water from flowing into the free section through the secondary construction joint between the protective cover and the grid beams, causing corrosion, and improves the safety of the ground (rock) anchor for the long-term.
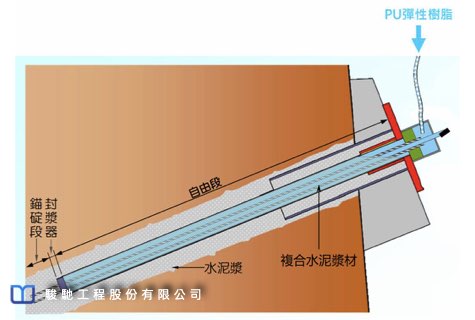
Groting Anti-Corrosion Technology For The Free Section Of In-Place Ground (Rock) Anchors
將下載檔案寄至:
・More Construction Result Sharing
Contact us:+886 2769-2355
Copyright ©Jines Construction Co.,Ltd