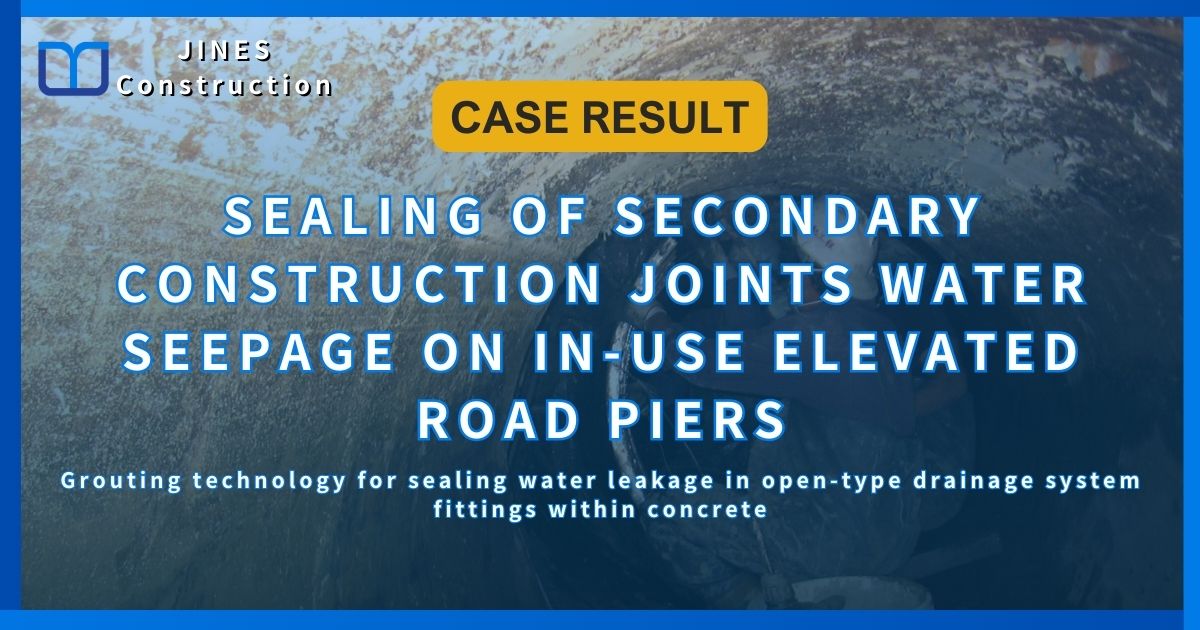
SEALING OF SECONDARY CONSTRUCTION JOINTS WATER SEEPAGE ON IN-USE ELEVATED ROAD PIERS
Grouting technology for sealing water leakage in open-type drainage system fittings within concrete
―
1. Project Background
After a period of use, the PVC pipe interface of the drainage system inside the concrete pier of an elevated road began to leak. During the rainy season, rainwater escaped along the PVC pipe interface and seeped through the surrounding area of the fittings into the construction joints of the concrete, resulting in streaks of water seepage and efflorescence on the surface of the pier, affecting its appearance.
To address the water leakage issue and prevent unnecessary public concern, the maintenance unit commissioned a professional contractor to draw up a sealing solution for the PVC interface and water seepage pathways. The proposed solution was submitted for review and approval before implementation.
―
2. Solution
Due to strict limitations on drilling and localized demolition on the piers of elevated roads in use, and the prohibition of pressure grouting to prevent damage to the concrete, coupled with the uncertainty of the leakage location at the PVC pipe interface, the difficulty of devising a solution was further compounded.
After collaborative discussion among various parties to formulate a solution, the following implementation principles were established:
(1) The use of long-lasting, low-viscosity grout for penetration sealing;
(2) Allowing the grout to naturally infiltrate the gaps and PVC pipe interfaces through gravity flow;
(3) Employing specially formulated ultra-slow setting grout to ensure thorough penetration into the gaps;
(4) During construction, grouting was to be conducted from the box girder water collection ports and had to continue until there was no further change in the level of grout material at the water collection ports;
(5) Construction activities could not disrupt traffic on the elevated road during the process.
―
3. Works Design
The main feature of this project was the use of gravity flow to fill the interfaces and surrounding gaps. During grouting, a low-viscosity ultra-slow setting grout was to be injected into the drainage pipes, and after maintaining for a certain period to allow natural infiltration into the gaps, precise control of initial setting time was implemented to facilitate the removal of any residual grout inside the pipes.
To accommodate the project’s characteristics, the construction design was outlined as follows:
(1) Utilization of a long-lasting type of low-sodium sodium silicate chemical grout (SSA) combined with aluminum silicate solution to prepare an ultra-slow setting dual-component grout
(2) Control of initial setting time of the grout between 3 to 6 hours, adjustable according to site conditions
(3) Before initial setting, the viscosity of the grout should not exceed 2 cP, to match the viscosity of rainwater (approximately 0.9 cP)
(4) Employment of vehicle-mounted mixing equipment along with a high-lift grouting pump to transport the grout from beneath the elevated bridge to the water collection ports of the box girder, avoiding disruptions to traffic on the elevated road
(5) Ensuring that the drainage pipes were fully filled with grout and promptly replenishing any gaps, allowing the grout to settle for 30 minutes after the liquid level stabilized at the water collection ports, utilizing hydraulic pressure to ensure thorough infiltration and filling.
If a sudden significant decrease in liquid level was observed during the process, continuous replenishment of grout to be conducted until the liquid level stabilizes, with continued monitoring for 30 minutes.
―
4. Works Process & Results
To ensure that the drainage holes were filled with grout while withstanding significant pressure (approximately 500 kPa) at the water outlets and cleaning ports, and to prevent any abnormal leakage of grout, expandable polyurethane resin was first used to fill the gaps around the outlets and cleaning ports.
Then, expandable rings were employed to seal the water outlets and cleaning ports, followed by mechanical compression plates on their exteriors, along with the use of quick-setting grout to fill any remaining gaps. This process ensured that the water outlets and cleaning ports did not experience any grout leakage, thus maintaining the effectiveness of the infiltration sealing.
The construction process progressed smoothly, and once the liquid level at each water collection port remained stable for over 30 minutes, indicating no significant decrease, the outlets and cleaning ports were immediately removed to prevent grout clogging the drainage pipes. Any remaining grout in the drainage system was flushed out, and the pipes were cleaned.
While the grout material used was non-toxic, efforts were made to recover as much of the residual grout as possible to avoid environmental contamination.
―
5. RESULTS
As drilling, localized demolition, and pressure grouting were prohibited for sealing treatment on the piers of elevated roads, a method utilizing ultra-slow setting chemical grout via gravity flow was employed.
Following completion of the works, continuous monitoring during rainy seasons and over several years of use revealed no recurrence of water seepage at the construction joints of the piers treated with chemical grout.
This successful outcome fully achieved the objective of sealing water seepage at the secondary construction joints of the piers of elevated roads in use.
―
・More Construction Result Sharing
Contact us:+886 2769-2355